- Home >
- Security and Safety Insights >
- The Journey to a Safe and Compliant Lockout Program
The Journey to a Safe and Compliant Lockout Program
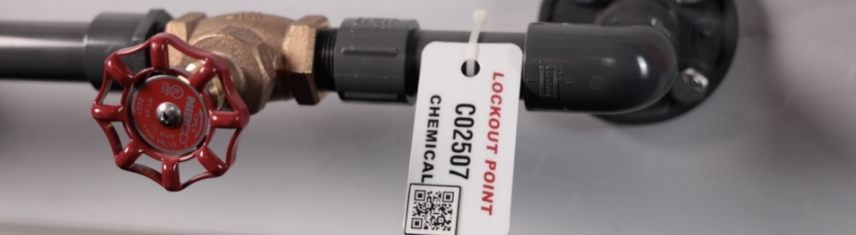
If you’re working on lockout tagout programs, you know how much is involved in making sure everyone gets to leave work safe and whole. Even if you’re confident you know all the key steps for lockout tagout—writing policies and procedures, selecting the best products, training and sustain your program—how confident are you in the order to take these steps in?
However, what many overlook is the importance of the order in which these procedures should take place to ensure a safe and successful lockout program.
Which of the Steps for Lockout Tagout Comes First?
Oftentimes, organizations want to jump right into training, which is essential to every lockout program. However, there is a lot of work that must be done before meaningful training can happen. By having an informed lockout policy in place first, you will be able to guide your training specific to your equipment and your organization's individual needs based on the type of lockout that is being done, and who is physically engaged in the lockout activity.
The proper steps for a lockout program
To be successful, you first need to understand what type of lockout you need and who is doing the lockout - your operator or group lockout. You also need to know what hazardous energy is on your equipment, so you can safely isolate it:
- 气动
- 电气
- Hydraulic
- Thermal
- Gravity
- Other hazardous energy
Once you have a comprehensive understanding of your organization's needs, then you can begin writing the lockout policies and procedures that will be the basis of your training program. They should spell out – step-by-step – what the roles and responsibilities of your authorized employees are specific to the lockout policy and equipment specific procedures. This will set your authorized individuals up for success with customized training designed specifically to your lockout activities.
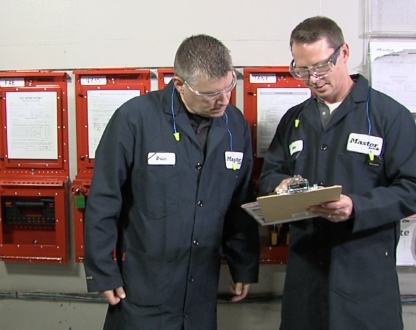
Why safety policies and procedures are important before training
Without policies in place, training would simply be based solely on reciting OSHA 1910.1471 and Canada's CSA-Z460:202, rather than customized to your organization, employees, and the equipment they are using.
This is important because hazardous energy is different depending on the type of equipment you are using. For example, the way you lock out an injection molding machine may be completely different from how you lockout a conveyor system based on the type of hazardous energy present. It’s essential to define how to secure each isolation point based on its unique properties, then train your employees accordingly.
Sustaining your lockout program
One of the biggest challenges organizations face with their lockout program is making sure that all of the work that they’ve put into policies, procedures, and training can be sustained and kept current. Changes like new equipment, modifications, and yearly reviews can complicate things, but they are inevitable.
It’s important that all changes are captured within your lockout policy, procedures, and training, as your business evolves – it’s truly the only way for your lockout management system to protect your employees’ safety and ensure your organization's compliance.
And, while this may feel like a never-ending process, there are a few tricks to help keep it more manageable. One great strategy is to consider including a periodic inspection sheet with your lockout procedure to note any changes in that lockout procedure.
If you do notice any differences or have a new piece of equipment or process, it's always important to note those changes to the one responsible for making changes to the lockout policy and procedure. This will ensure that everyone understands how to incorporate them into your lockout training program.
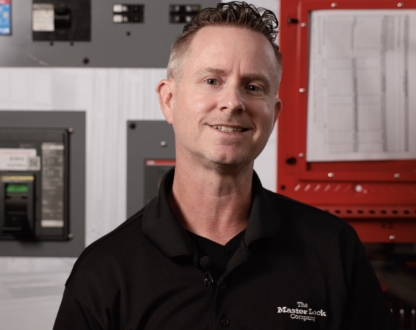
Enlisting the help of a third party
It’s easy to feel overwhelmed when maintaining your program – especially, when you have so many other important responsibilities on your plate. Maintaining all the documentation, periodic inspections, changes in processes, and reflecting them in your policies, procedures, and training program, takes knowledge, extra capacity, time and meticulous management.
That’s when third-party resources with customized, efficient processes, and expertise, like Master Lock, can help support you. We can help you identify gaps in your lockout management system to develop lockout policies and procedures, and help maintain all of your important documentation as well as provide you with customized training, so you can focus on all the rest.
Explore how third-party resources like Master Lock can help you on your journey to a safe and compliant lockout program.